Quality Rotational Molding
Quality Rotational Molding
Rotational molding is a manufacturing process where plastic is melted, rotated in a
mold to coat evenly, cooled, and removed, creating hollow, seamless products.
BUILT WITH YOU IN MIND
BUILT WITH YOU IN MIND
Whether you need one of our services or all of them, we are here to help.
Whether you need one of our services or all of them, we are here to help.
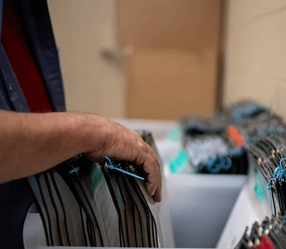
DESIGN &
ENGINEERING
Integrity can offer you the design and engineering support you need such as:
- Conceptualize your product.
- Coordinating full product design.
- Coordinating new tool design.
- Monitor tool building process to ensure top-quality tooling, best price, and on-time delivery.
- Quality control to make sure all finished products meet required specifications.
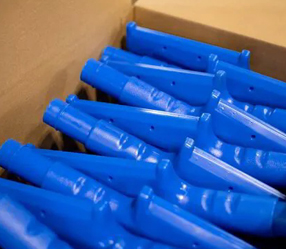
ASSEMBLY & PACKAGING
Integrity offers complete pack-out and assembly services:
- Inserts, fillings, foam fillings, and multi-layer products.
- Handles, hardware, and fittings.
- Dropshipping directly to your customers.
- Shipment to distribution centers.
- Overseas shipping.
- Stocking programs.
WE OFFER EVEN MORE
WE OFFER EVEN MORE
Secure Mold Storage
We will keep your molds safe and secure at our facility.
Quality Control
We will make sure all your products are thoroughly reviewed before shipment to you or your customers.
Design Packaging
Need help designing your packaging? We got you.
Quality Control
Need us to bar code products before they leave? We can do that too.
THE ROTATIONAL MOLDING PROCESS
How It Works – SUCCESS IS IN THE PROCESS
How It Works – SUCCESS IS IN THE PROCESS
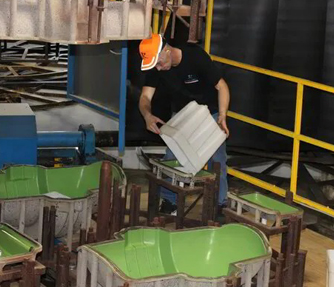
Loading Stage
The rotational molding process starts when a quality mold is placed on one of the arms of the rotational molding machine. Several molds may be placed on the machine at the same time. Pre-measured plastic resin is then loaded into each mold.
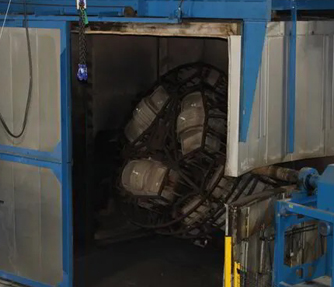
Heating Stage
The molds are then moved into the oven where they are slowly rotated on both the vertivcal and horizontal axis. The molding resin begins to coat the internal surface of the heated mold evenly which allows the operator to control the wall thickness.
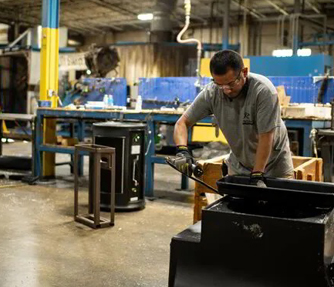
Controlled Cooling Stage
Once the mold rotates from the oven to the cooling chamber, the curing process begins. The curing process is a combination of air and water that are applied to the mold to help bring the overall temperature down to a pre-determined specification.
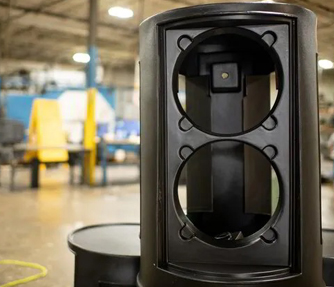
Finishing Stage
Once the mold reaches its pre-determined temperature, the product is then unloaded from the mold and moved to the finishing area. In this stage the products are manually trimmed, inspected by our quality control team, and a glossy finish can be applied if desired.
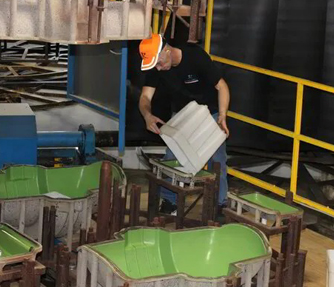
Loading Stage
The rotational molding process starts when a quality mold is placed on one of the arms of the rotational molding machine. Several molds may be placed on the machine at the same time. Pre-measured plastic resin is then loaded into each mold.
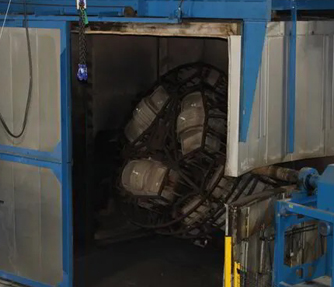
Heating Stage
The molds are then moved into the oven where they are slowly rotated on both the vertivcal and horizontal axis. The molding resin begins to coat the internal surface of the heated mold evenly which allows the operator to control the wall thickness.
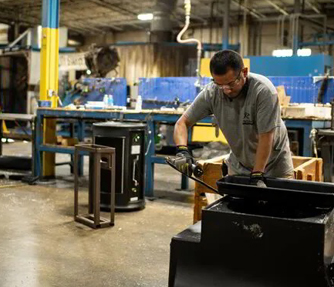
Controlled Cooling Stage
Once the mold rotates from the oven to the cooling chamber, the curing process begins. The curing process is a combination of air and water that are applied to the mold to help bring the overall temperature down to a pre-determined specification.
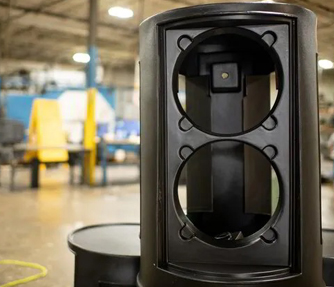
Finishing Stage
Once the mold reaches its pre-determined temperature, the product is then unloaded from the mold and moved to the finishing area. In this stage the products are manually trimmed, inspected by our quality control team, and a glossy finish can be applied if desired.
WANT TO LEARN MORE ABOUT THE ROTATIONAL MOLDING PROCESS?
We would love to talk with you more about our process or give you a tour of our facilities.