Rotational Molding F.A.Q’s.
Rotational Molding F.A.Q’s.
Rotational molding is a manufacturing process where plastic is melted,
rotated in a mold to coat evenly, cooled, and removed, creating hollow,
seamless products.
Frequently Asked Questions
Frequently Asked Questions
These are just a few of the questions we often get asked.
THE ROTATIONAL MOLDING PROCESS
How It Works – SUCCESS IS IN THE PROCESS
How It Works – SUCCESS IS IN THE PROCESS
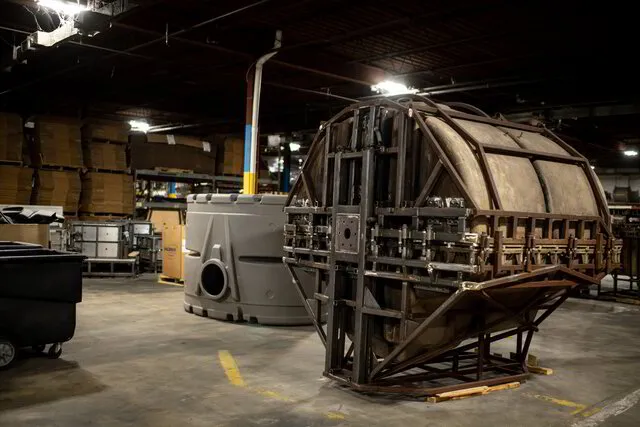
Loading Stage
The rotational molding process starts when a quality mold is placed on one of the arms of the rotational molding machine. Several molds may be placed on the machine at the same time. Pre-measured plastic resin is then loaded into each mold.
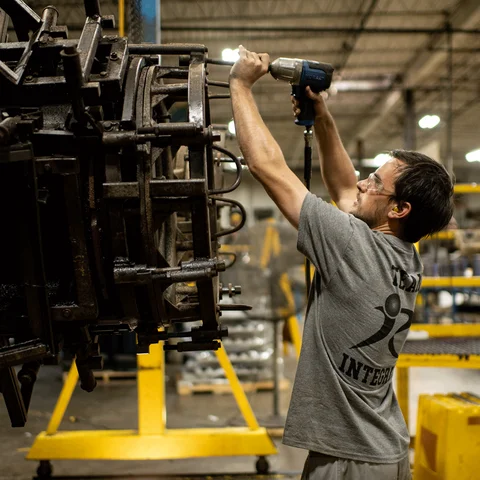
Heating Stage
The molds are then moved into the oven where they are slowly rotated on both the vertivcal and horizontal axis. The molding resin begins to coat the internal surface of the heated mold evenly which allows the operator to control the wall thickness.
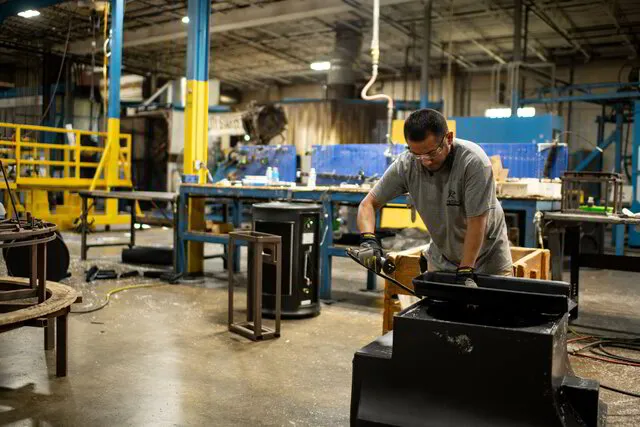
Controlled Cooling Stage
Once the mold rotates from the oven to the cooling chamber, the curing process begins. The curing process is a combination of air and water that are applied to the mold to help bring the overall temperature down to a pre-determined specification.
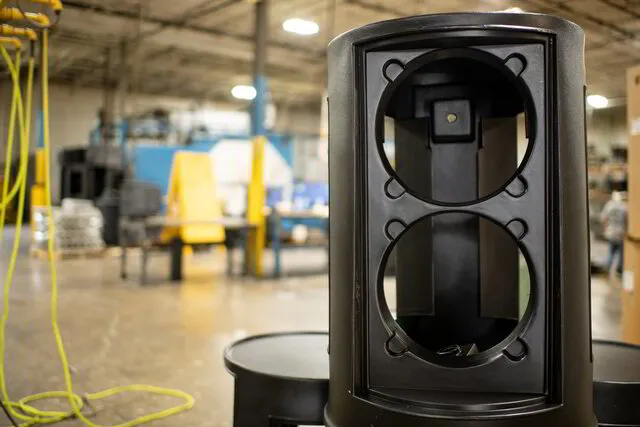
Finishing Stage
Once the mold reaches its pre-determined temperature, the product is then unloaded from the mold and moved to the finishing area. In this stage the products are manually trimmed, inspected by our quality control team, and a glossy finish can be applied if desired.
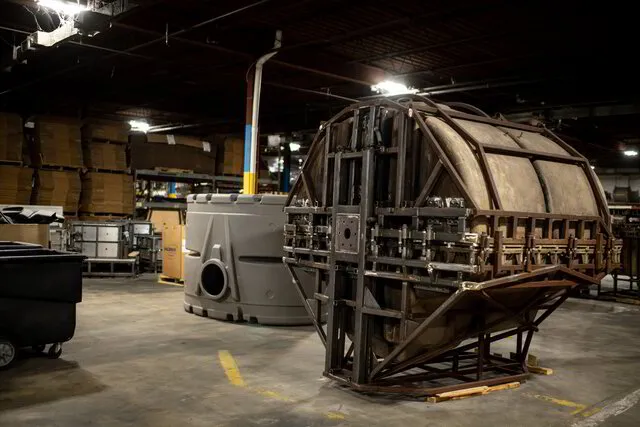
Loading Stage
The rotational molding process starts when a quality mold is placed on one of the arms of the rotational molding machine. Several molds may be placed on the machine at the same time. Pre-measured plastic resin is then loaded into each mold.
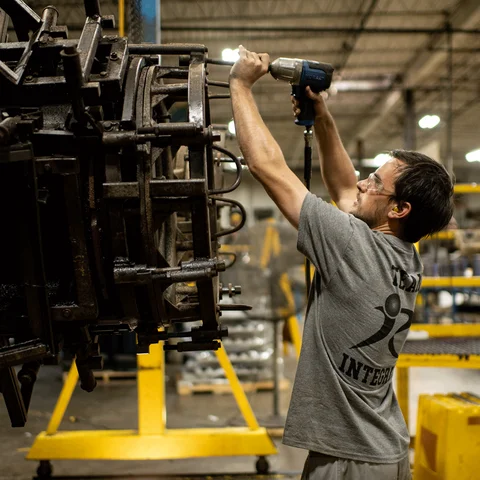
Heating Stage
The molds are then moved into the oven where they are slowly rotated on both the vertivcal and horizontal axis. The molding resin begins to coat the internal surface of the heated mold evenly which allows the operator to control the wall thickness.
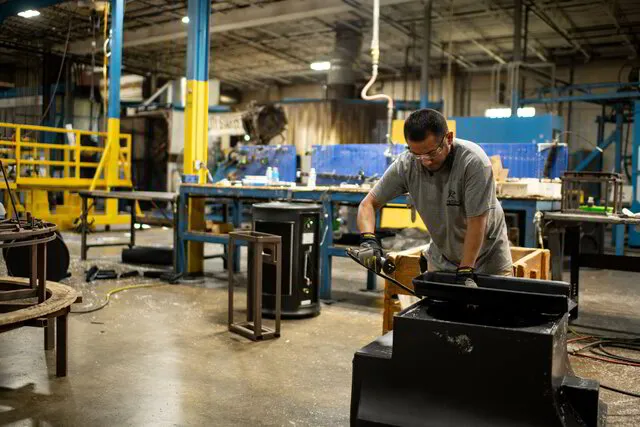
Controlled Cooling Stage
Once the mold rotates from the oven to the cooling chamber, the curing process begins. The curing process is a combination of air and water that are applied to the mold to help bring the overall temperature down to a pre-determined specification.
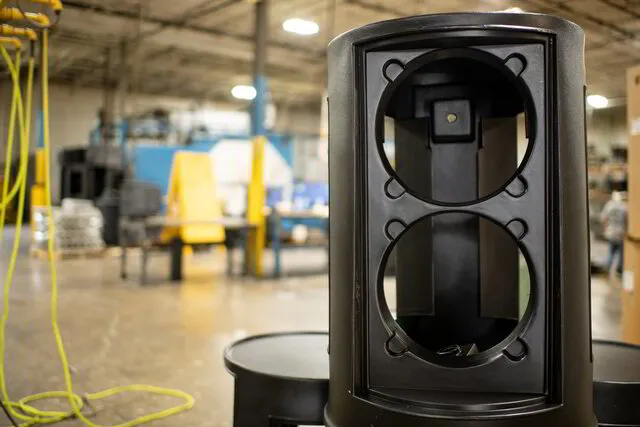
Finishing Stage
Once the mold reaches its pre-determined temperature, the product is then unloaded from the mold and moved to the finishing area. In this stage the products are manually trimmed, inspected by our quality control team, and a glossy finish can be applied if desired.